- The Essential Guide to Digital Transformation
Chapter 5
Why Digitization is Essential?
Date:
4 April, 2024

What is driving companies to digitalize?
Communication Platform
Some firms have engaged to some degree in platform strategies, in an attempt to redefine their industry’s value chain so customers and suppliers can interact more directly and benefit from network effects. Platforms have the power to radically alter the way value is distributed in a value chain.
New Marginal Supply
Many firms were using digital technology to tap into previously inaccessible sources of supply at a marginal cost. Examples include the Swedish retailers H&M and Ikea, both of which are offering a online reseller options for their own customers, allowing them to sell used, branded products to one another.
O2O Products and Services
Many companies were using digital technology to create new products or services with digital features combination with mobile applications, typically to serve new demand with additional value to their customer. One example is P&G’s Oral-B toothbrush with Bluetooth-enabled digital guidance.
Rebundling and Customizing
A lot of companies are using digital technology to rebundle their products or services to better serve their existing customers. The paywall for news content erected by the New York Times where people can personalize reading lists and organize the content they read is a good example.
Digital Distribution Channels
Many firms invested in digital distribution channels, in an attempt to make it easier for customers to access their products or services. This include building an e-commerce platform or making integration with popular online shops. As online purchase are becoming a norm these days for many customer.
Cost Efficiency
Many companies were using digital to improve their cost efficiency, typically through automation or cost scaling. In an age where operational excellence is the norm, this strategy looks like it’s aimed at survival with lower overhead rather than creating a source of comparative advantage.
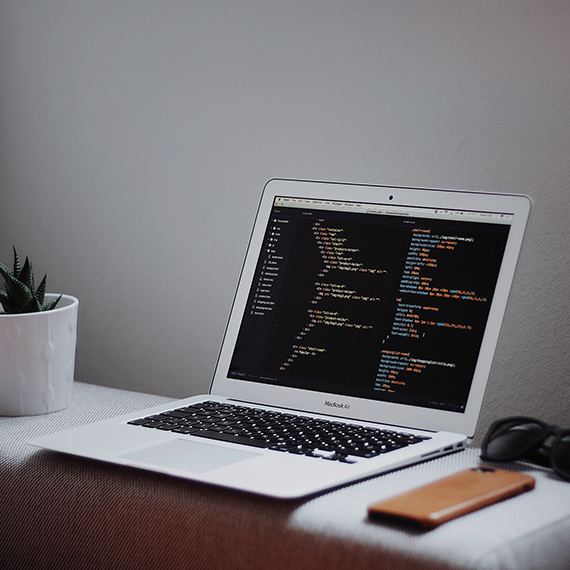
New Technologies Create a “Solutions Gap”
As with any new wave of technology, another challenge emerges for businesses. When new technology is created and introduced into the market, there’s typically a disconnect between the vendors who sell the core technology (such as hardware, software, or cloud services) and the enterprise customers who can benefit from them. While the technology itself is compelling and business leaders can see their potential in transforming their operations, a gap remains in terms of understanding how to effectively implement them in their organizations. We call this disconnect the “solutions gap.”
Discover MoreThe Essential Guide to Digital Transformation
The world has gone digital, and there’s no going back.
Read More